- Springs
- Spring U-Bolts
- Drum Brake Shoes
- Brake Drums and Brake Discs
- Landing Gears
- Fifth Wheel Couplings
- Shock absorbers
- Hubs
- Rods and Rod Ends
- Body parts
- Slack adjusters
- Mirrors
- Brake Chambers and Spring Brake Chambers
- Caliper repair kits
- Bolts and Nuts
- Brake Camshafts and Brake Camshaft Repair Kits
- Cab tilt pumps and cylinders
- Air valves
- Water pumps
- Trailer cables and connectors
- Rubber Metal Parts
- Air brake compressors and repair kits
- Drive belt tensioners and rollers
- Fan clutches
- Radiators
- Drive belts
Drum Brake Shoes
The break shoe surface is covered with the E-coat, a durable electrophoretic coating. E-coat is paint layer applied to a surface by electrodeposition. As a result, the E-coat-treated brake shoe obtains high corrosion resistance and high paint strength.
High Wear-Resistance and Destruction Resistance of the Shoe Design.
High Wear-Resistance and Destruction Resistance of the Shoe Design
The MARSHALL drum brake shoes are made of thermo mechanically treated steel. Thermomechanically treated material is characterized by increased durabilit , so parts made of such kind of steel are less susceptible to crack being loaded, so premature failure is prevented, break shoes are more wear-resistant and have a long service life.
Shoe Contact Surfaces Strength
Shoe and roller junctions undergo special induction hardening process. When coming in contact with stronger parts (rollers), ordinary drum shoes wear and strain faster. Induction hardening (up to HRC 35-45), performed on the MARSHALL drum shoes, allows to prevent holes deformation and contact fatigue failure under various overloads.
Shoe Weld Strength
Manufacturing of the MARSHALL drum brake shoes CO2-shielded arc welding, which guarantees shoe strength, namely, absence of cracks and weld continuity and prevents deformation of shoe webs.
Perfect Fit
Conformance to required rivet hole sizes is strictly controlled. As a result, they don't have flaws, such as out-of-roundness and stretching, which, in turn, reduces the risk of poor shoe installation and loss of rivets during operation
Adherence to all above mentioned stages of production ensures performance stability of the MARSHALL brake shoes during entire service life.
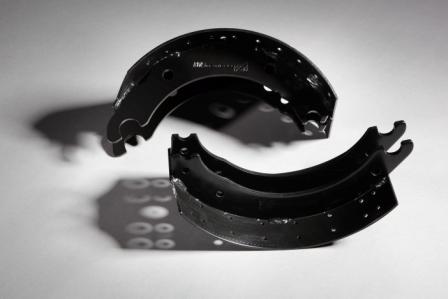
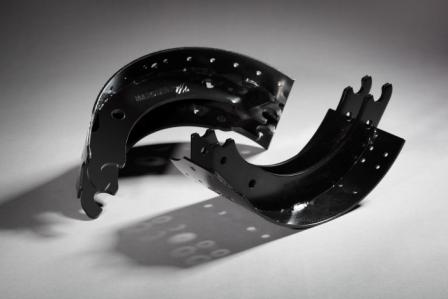